The Future of Robotics in Manufacturing
Manufacturers can increase throughput and product quality with the aid of robots. In contrast to gloomy stereotypes, technology enhances human workers' performance rather than replacing them. Robots can securely work alongside people thanks to technologies like machine vision and safety sensors. Small and medium-sized firms may now afford industrial automation because to declining robotics costs.
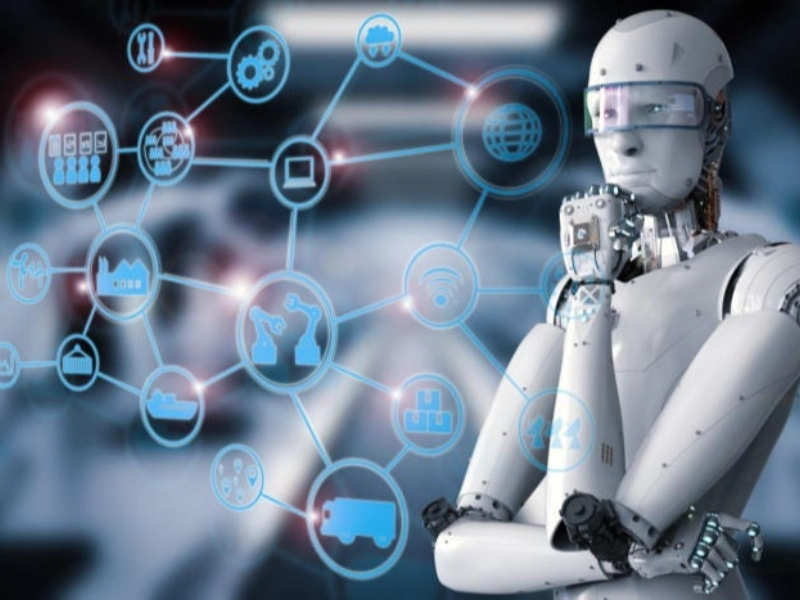
1. Intelligent robots will be available
Robots are intelligent enough to adjust to shifting factory conditions. They are also able to operate consistently and dependably since they are not distracted by the same things that humans are. Quality and productivity both rise as a result. Because of their preprogramming and incapacity to suffer from the attentiveness decrement that occurs in humans who execute repetitive activities repeatedly, they are less likely to make mistakes. They are therefore an excellent tool for jobs involving inspection and quality assurance. Nevertheless, integrating new technology necessitates that businesses employ knowledgeable support personnel to operate and maintain the devices. Manufacturers who want to use robotics may find this expense prohibitive. RaaS, or robotics as a service, is growing in popularity because it enables firms to take advantage of robotics process automation without having to make the original investment.
2. Robots will cooperate more
Cobots and humans can work together to accomplish difficult or sensitive jobs, which lowers human error and increases output. This is particularly helpful for intricate or risky production tasks like soldering. Collaborative robots will be used by more manufacturers in the future for jobs including maintenance, reprogramming, and inspection. They will be able to cut expenses and raise production and efficiency as a result. Furthermore, compared to people, collaborative robots are less prone to RSI (Repetitive Strain Injury) and are capable of working in confined areas. This is especially crucial in the electronics industry since even one mistake can lead to a complete product failure. This additionally liberates significant floor area for additional procedures that would necessitate a larger work area. This will speed up the process of recovering the cost of the robot investment and help lower inventory and shipping delays.
3. More autonomy for robots
These days, robots are able to pick up on environmental cues and modify their behavior accordingly. AI, industrial networking, and sensor technology make these capabilities possible. Autonomous robots can carry out structured, repetitive activities in production, freeing up humans to concentrate on more skill-based and critical thinking work. Additionally, they can be used to finish jobs that pose a risk to human workers. Businesses create specialized robotic systems for one or a small number of use cases. Although these tailored robot systems may cost more initially, they are less expensive to run than traditional manufacturing robots. Because of this, small and medium-sized manufacturers can afford them. They have the ability to work continuously without the need for lunch breaks, holidays, or vigilance decrement, which is a regular occurrence among employees that execute repetitive, normal jobs.
4. More flexibility for robots
More manufacturing flexibility is made possible by modern robotics systems, which can also adjust to shifting consumer expectations and aging populations. Businesses may create bespoke items as efficiently as mass production by utilizing modular robots with interchangeable components. It is now simpler to educate a robot to perform new tasks because to developments in robotic motion control. Robots may now be given directions vocally thanks to improvements in voice recognition technology, while AI-powered self-navigation and environment assessment are made possible by more sophisticated software processes. Furthermore, when performing repetitive activities, human workers undergo a loss in focus known as "vigilance decrement," which is not experienced by robots. This enables them to consistently produce faultless outcomes. Productivity, quality, and consistency all rise as a result. It also saves on the price of onboarding new hire training.
5. The cost of robots will decrease
Robots are now far more accessible and economical for small-to medium-sized manufacturing businesses. As technology develops, costs will keep dropping. Robotics dependability boosts industrial uptime, which raises productivity levels. This is particularly valid for businesses that use human labor in their manufacturing. Unexpected downtime in production lines can be caused by a variety of circumstances, including worker vacations, sick days, and injuries. Furthermore, floor space can be saved by programming robotics systems to operate in cramped areas. They are therefore helpful in warehouses, where robots are used by online retailers and logistics firms to stack boxes, retrieve things, and even make local deliveries. These robots also employ a technique called echolocation—which is how bats and dolphins use sound to determine distance—to sense and maneuver around humans.