The Future of Robotics in Manufacturing and Industry
The slow development of the economy and shifting demographics are pushing firms to invest in automation. Robotics integration and installation into production systems are becoming simpler thanks to developments in software development, processing power, and networking technologies. On the production line, collaborative robots assist people in carrying out operations that need for human supervision in a safe manner. Artificial intelligence is used by autonomous mobile robots to navigate their environment, which makes them perfect for material handling.
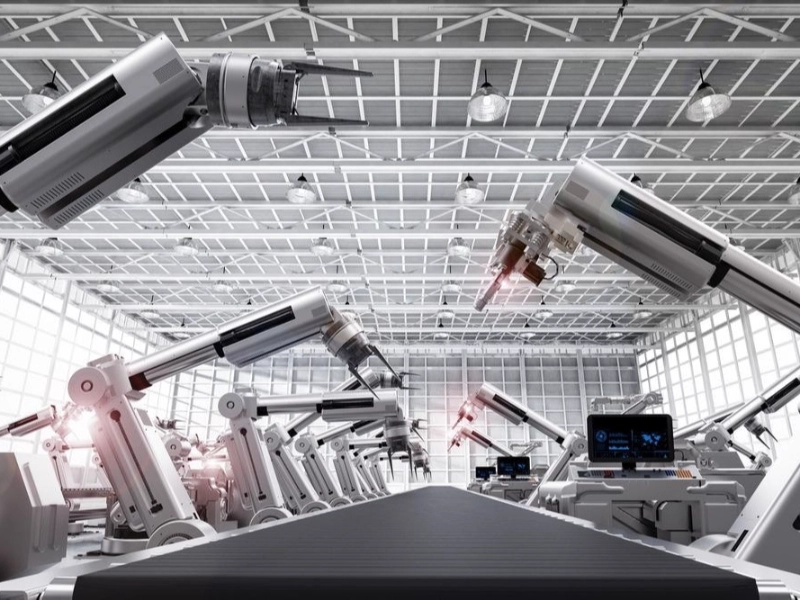
The Robotics Future
Many sectors have welcomed the use of robots. Robots coexist with humans everywhere, from laborers in factories and warehouses to nurses, doctors, and even police dogs (like the metal ones made by Boston Dynamics). Simple, repetitive operations are carried out by industrial robots. They are employed in manufacturing jobs such as welding, picking, and packaging. Robots are ideal for assembly lines and other repetitive occupations because they can perform repeated tasks faster and error-free than human workers. Safety sensors, which guarantee that robots may safely engage with humans in their workspaces, are also seeing growth in the market. Technological developments such as 3D embedded vision and multispectral and hyperspectral photography will enable robots to see and adjust to changing work situations.
Cooperative Automata
When we imagine robots in production, we usually see large mechanical arms filling hundreds of food packages per minute, soldering electronics, or assembling cars. Barriers such as fences keep humans and these industrial robots apart. A new type of robot called collaborative robots, or cobots, is made to operate closely with people without the need for boundaries or other safety precautions. They are built with rounded corners and smooth designs to disperse forces in the case of an unintentional collision. They also contain sensors to prevent accidents and power and force limitation to lower the danger of injury. By automating tedious or hazardous jobs, cobots can save labor expenses and increase production rates. Additionally, they enable staff members to focus on more important duties rather than tedious manual inspections and quality control.
Mobile Autonomous Robots
Industrial robots have typically only been used in stationary, workstation settings. Physical barriers, light curtains, and area scanners that give people a limited window of time to avoid them before the device shuts down are used to keep humans away from them. This paradigm is altered by autonomous mobile robots, which enable robots to navigate manufacturing facilities independently. As a result, businesses can benefit from leaner, more dynamic workflows without having to alter existing production facilities or warehouses to make room for process automation. In order to access equipment and parts that are difficult to reach in dangerous or distant locations, these vehicles can also carry payloads like inspection kits. By maintaining low latency connection with the factory floor, these vehicles are able to maximize batch quality and waste control in addition to choosing the optimal path for faster production.
Lighting-Off Production
Although it may seem like a pipe dream, manufacturers are starting to consider lights-out manufacturing as a way to cut down on labor costs on the factory floor. While labor-intensive and physical tasks are being automated, some jobs are better suited for human workers. People with the necessary expertise are needed, for instance, to train automated machinery to follow a complex design or assembly. Industrial robots can monitor their own performance and identify problems that need human intervention by using Internet of Things (IoT) smart technologies. By lowering labor expenses and utility bills, these preventative maintenance procedures not only cut production costs but also increase efficiency. By using high-frequency data adapters to track the health of their machines, manufacturers can reduce total operating costs by anticipating future breakdowns and optimizing maintenance plans.
Using IoT to Connect Industrial Robots
Industrial robots can gather and send data for use in upcoming manufacturing through a networked system. These data will contribute to the enhancement of robot performance, quality, and capabilities. Both the final user and the robot maker will gain from this. Conventional industrial robotic systems carry out a restricted range of repetitive operations, like product spray painting or adhesion. Because modular robots have interchangeable parts, they allow for bulk customisation and allow manufacturers to produce custom orders in larger quantities and at a lower cost. This growth is mostly being driven by lower maintenance costs and the simplification of the engineering process through virtual validation and simulation. This pattern is anticipated to persist. In the end, robotics technology will revolutionize production methods and contribute to job growth.